Slim onderhoud alsmaar goedkoper. “Het potentieel is enorm!”
Betaalbare sensoren zorgen voor een shift van periodiek naar conditioneel onderhoud, waardoor maakbedrijven een pak geld kunnen besparen. In de industrie 4.0-proeftuin ‘Smart Maintenance’, die de Vlaamse overheid via VLAIO organiseert, demonsteren Flanders Make en imec hoe dat juist werkt voor het meten van schade aan lagers, cruciale onderdelen in elk machinepark. Projectleider Steven Devos (Flanders Make) gidst ons door de basics.
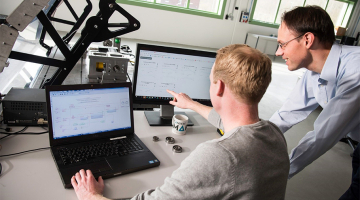
“Veel bedrijven zetten vandaag belangrijke stappen op het vlak van connectiviteit”, weet Steven Devos. “Niet alleen door hun producten en productieprocessen uit te rusten met sensoren, maar ook door data uit andere bronnen, zoals controllers van PLC-sturingen, te centraliseren. Dat levert een hoop inzichten op, waarmee ze hun bedrijfsprocessen en service kunnen verbeteren.”
Van periodiek naar conditioneel onderhoud…
Zeker op het vlak van onderhoud is er nog een enorm potentieel, stelt Devos. “Door hardware en software toe te voegen, kunnen maakbedrijven de stap zetten van periodiek onderhoud volgens vaste intervallen, naar conditioneel onderhoud op basis van de werkelijke toestand van machineonderdelen. Zo verlagen ze de onderhoudskosten én verhogen ze de productiviteit van hun onderneming.”
… vanaf 50 euro
Deze ingrijpende shift wordt verder aangezwengeld door de beschikbaarheid van betaalbare sensoren. “In een vorig project hebben we vastgesteld dat we met een accelerometer (trillingssensor, red.) van 50 euro al in staat zijn om schade aan lagers te detecteren. De voornaamste technische vereiste is de bandbreedte: deze moet hoog genoeg zijn om de hoge frequenties te registreren van eventuele tikken die wijzen op schade. Bijvoorbeeld de impact van een kogel die door een minuscuul putje rolt.”
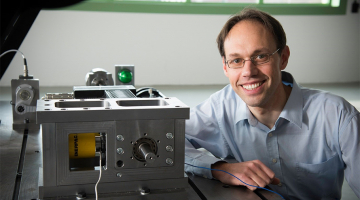
Live demo
De proeftuin ‘Smart Maintenance’ demonstreert op kleine schaal hoe bedrijven de stap kunnen zetten naar het conditioneel onderhoud van lagers. “We hebben een testopstelling ontwikkeld om versneld lagerschade te meten op basis van data van machines in uiteenlopende omstandigheden. Zo verkleinen we de kloof tussen lab en werkvloer en ontstaan betrouwbare modellen voor het plannen van onderhoudswerken”, zegt Steven Devos.
Interesse in deze demonstratie? Mail naar Steven of bel +32 498 91 94 18.
Unieke combinatie
In de praktijk zijn er nauwelijks betrouwbare data voorhanden. “Lagers zijn dan ook ontworpen om zo weinig mogelijk te falen”, zegt Steven Devos. “Stel dat een lager pakweg twee jaar meegaat, of ongeveer een miljard omwentelingen: als er dan eens een fout optreedt, is de kans klein dat een bedrijf juist die machine heeft uitgerust met een monitoringsysteem. Bovendien zijn de operationele condities meestal niet bekend. Hoe weet je bijvoorbeeld honderd procent zeker dat de operator een bepaalde lager heeft gesmeerd volgens het onderhoudsplan?”
Die unieke combinatie van enerzijds relevante foutmetingen en anderzijds gekende operationele omstandigheden maakt deze proeftuin dubbel interessant.
Eén fout per dag
Gelukkig duurt het in het labo van Flanders Make geen twee jaar om een fout te meten. Dankzij eerder opgebouwde ervaring slagen de onderzoekers erin om binnen de acht uur een fout te genereren.
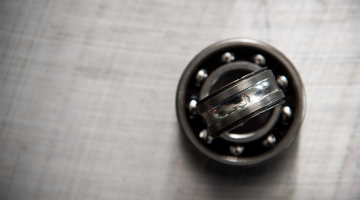
“Daarvoor manipuleren we verschillende parameters”, vertelt Steven Devos. “Ten eerste kunnen we de beginschade van de lager kleiner of groter maken. Ten tweede kunnen we de belasting regelen, dus de kracht die op de lager uitgeoefend wordt. En ten derde kunnen we variëren we met het toerental.”
Tip: binnen deze proeftuin kan je datasets op maat laten ontwikkelen. “Er is al een bedrijf dat ons heeft gevraagd om 25 lagers te testen in vijf verschillende omstandigheden”, aldus Steven Devos.
7 parallelle testopstellingen
Momenteel is er één testopstelling voor het versneld meten van lagerschade operationeel. “Tegen de zomer breiden we onze infrastructuur uit naar zeven testopstellingen, die we parallel kunnen laten werken en waaruit we automatisch data kunnen extraheren”, zegt Devos. “Zo verzamelen we niet alleen snel data, maar leren we ook hoe identieke opstellingen zich toch anders kunnen gedragen.”
Het verwerken van de data gebeurt in de cloud, waarvoor imec de nodige expertise aanreikt. “Die gedistribueerde aanpak is hier niet per se nodig omdat alle testopstellingen op één locatie staan, maar voor bedrijven is dit wél interessant. Zo kunnen ze data capteren van machines op verschillende locaties in de wereld.” De cloudtechnologie van imec laat hierbij toe om op een schaalbare, beveiligde manier datastromen afkomstig van de testopstellingen op te slaan en te delen met gelegitimeerde gebruikers en toepassingen.
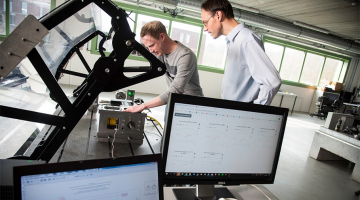
50.000 metingen per seconde
Een van de uitdagingen van deze proeftuin, was het verwerken van de ruwe meetdata tot nuttige en bruikbare informatie. “In het begin hebben we ruwe data aan 50 kilohertz naar de cloud gestuurd met een overbelaste server als resultaat”, lacht Steven. “Dat was dus niet werkbaar. Daarom hebben we een algoritme ontwikkeld om die 50.000 metingen per seconde om te zetten naar één getal dat de gezondheid van de lager weergeeft.”
Relevante parameters
Grote technische obstakels waren er niet voor deze proeftuin. “De testopstellingen zijn vooral een kwestie van good engineering practice”, stelt Steven Devos. “De uitdaging voor ons is vooral dat we de verschillende operationele condities zo goed mogelijk willen kennen én dat we willen weten parameters relevant zijn en welke niet.”
Tip: ook deze industrie 4.0-proeftuinen draaien momenteel op volle toeren.
“Twee opstellingen zijn nooit identiek, al was het maar omwille van de tolerantie van de as waarop je de lager monteert. Als een as één honderdste van een millimeter afwijkt, kan het dat de spanning op de lager toeneemt en is dat dus een relevante geometrische parameter. Maar voor een opstelling met meer dan twintig onderdelen is het onbegonnen werk om met al die informatie rekening te houden. Wij willen nu achterhalen waar de grens juist ligt. Welke parameters relevant zijn en welke minder, zodat we ook bedrijven hierrond kunnen adviseren.”
Lerende machines
Om op termijn nog betere onderhoudskeuzes te maken, werkt imec in het kader van deze proeftuin ook aan machine learning. “Als de volledige testinfrastructuur operationeel is, willen we demonsteren hoe de verschillende testopstellingen van elkaar kunnen leren”, zegt Steven. “Hoe meer zekerheid je hebt over de nog te verwachten resterende levensduur van een lager, hoe beter je beslissingen kan nemen. Wacht je bijvoorbeeld nog even of plan je tóch een onderhoudsbeurt in.”
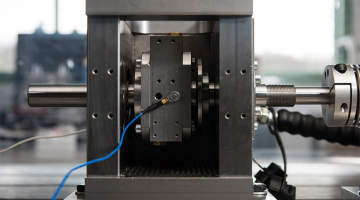
Een greep uit het aanbod
Deze proeftuin is interessant voor machinebouwers, onderhoudsbedrijven en aanbieders van technologie voor het onderhoud van machines. En bij uitbreiding voor alle productiebedrijven die machinedata willen capteren.
“Wij kunnen datasets aanleveren waarmee ze onmiddellijk hun processen kunnen optimaliseren”, zegt Steven Devos. “Verder kunnen we hen adviseren bij het aankopen van hardware, zoals sensoren en de bijhorende data-acquisitiesystemen. We helpen hen daarnaast ook bij het kiezen of ontwikkelen van geschikte software om de meetdata te verwerken.”
In een latere fase is het ook de bedoeling om vanuit de proeftuin bedrijven concreet te adviseren op het vlak van cloudinfrastructuur, machine learning en het visualiseren van de verwerkte data.
Contacteer Steven om de mogelijkheden voor jouw bedrijf te bespreken!
Vragen rond Industrie 4.0?
Heb je ondertussen vragen rond industrie 4.0 in Vlaanderen? Laat van je horen op industrie40@vlaio.be.
Abonneer je hier op onze VLAIO nieuwsbrief en ontvang elke 2 weken de nieuwste tips rechtstreeks je mailbox.